Insert Molding
Insert molding is suitable for assembling metal and plastic parts quickly and smoothly. We can design and manufacture all the components in-house and also insert-mold for you.
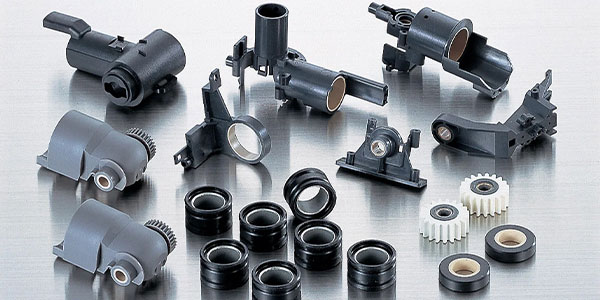
Insert Molding Service for Plastic Parts
LXL Molding is an industry leader in the insert molding service sector, having been around since 1978. The one mission we have is to provide cost-effective manufacturing solutions for various manufacturers in the same product line.
We have clients spread out worldwide, more proof of the quality of our mold products. We serve a wide range of industries from Furniture, Home Appliance, Baby Products, Automobiles, Warehouses and Storage, and Buckets. We are expanding our global network to reach more clients in new places.
Advantages of LXL Molding's Insert Molding
At LXL Molding, insert molding is a core process that we use to create all kinds of products for our varied clientele base.
Choosing to work with us opens you to a number of benefits, and some of these advantages include the following.
- Reduced Assembly Costs:
Our processes are the cheapest in the market, and you still get high-quality insert molds. We handle the entire process from inception to production at discounted prices as we understand businesses need some room to breathe once in a while.
- Completion of Complex Parts:
Through the use of the latest technologies and machinery, we are able to produce complex parts without any trouble with blinding speeds. All you have to do on your end is to provide the blueprints.
- Flexible use of Material:
We can work with all kinds of materials to bring your concepts to life. We have state-of-the-art machinery and a qualified working staff that know exactly what they are doing, and this ensures you get what you order.
- High-Efficiency:
We have a team of qualified staff trained in all forms of the insert molding process. They will handle the product’s design and walk with you through the whole journey until the products are ready.
About Insert Molding
What is Insert Molding
Insert molding is defined as a variation of injection molding techniques that involves the insertion of a metal part into a mold before the actual injection molding. This insertion can be done manually or by an automated process through the use of a robotic arm. Once the insertion is completed, the mold is closed, and plastic is molded over the insert to transform the different parts into a single component.
Insert molding doesn’t follow a certain standardized method; there are many ways that one can approach the process and make it work best for their needs. You can use it for simple designs like making electrical insulations to more complex designs that are used in advanced manufacturing processes like the automotive and aerospace industries.
What makes insert molding such a handy option is the fact that it eliminates the need to use extra parts just to join other parts when you need to form a single component. It is a cheaper and firm securing method that ensures there are no structural weaknesses in the joints, something that usually causes problems for other forms of joints.
Molding production through this method also cuts down the labor and energy costs as you are effectively handling a job that could have needed the production of many items by many hands using a lot of electrical energy in the process. In a way, it is a cost-effective technique that not only gets things done at twice the speed but halves the expenses that go into the entire production line.
Insert Molding Process
The insert injection molding process is a pretty straightforward process that takes place through four distinct phases.
- Clamping: The mold, the part into which the molten material is injected into, is secured and clamped tightly. This is important because the resulting shape and size of the end product will depend on the state of the mold. Therefore, caution has to be observed that everything is exactly how it should be in this stage; otherwise, the entire process that follows will be compromised.
- Injection: The molten material is then injected into the waiting mold while being subjected to more heat and pressure for uniformity. The injection has to be done quickly to stop the material from starting to cool while the injection is still in progress, as that will affect the structural integrity.
- Cooling: Once the injection material has filled up the mod to the needed capacity, the cooling process begins. Some shrinkage is expected in this process, and for this reason, most people usually add some extra injection before cooling starts to make up for the difference.
- Ejection: Once sufficient time has passed and the cooling has progressed nicely, the solidified model can now be ejected from the mold using an ejection system. This can be tricky since the finished product tends to stick to the mold after cooling; the ejection system has to be strong and clean enough to not damage the mold.
Precision Mold Design for Insert Molding
When it comes to insert molding, precision is everything because the end product depends on that more than any other thing. The precision has to begin from the very top with the camping process to the ejection point. It is for this reason that there’s a lot of investment that goes into setting up theinsert molding infrastructure.
At LXL Molding, we always try our all to ensure that nothing that comes off our assembly line is defective. We have invested in advanced molding technologies in combination with state-of-the-art machinery that ensures there’s very little room for errors. We also have a team of qualified designers and engineers who work together to bring concepts to life no matter how complex they may be. We understand that the designed products we mold are used in industries that value safety and performance above everything else, and that’s the reason why we value precision.
Insert Molding Materials Options
There are a number of options when it comes to insert molding materials that are used in the injection molding process. The choice of material used is guided by factors like the nature of the end product, the cost of production, and the availability of the raw material in question. The most notable ones that are used widely in the manufacturing industry the following.
- PP
- PE
- POM
- PMMA
- ABS
- PA6
- PVC
- PLA
- PC
- Nylon
- PS
Applications of Plastic Insert Molding
Insert Injection mold products are utilized in both the domestic and commercial spaces in varying ways. The following are some of the notable plastic insert moldings.
- Medical Devices: Medical devices and instruments have to be precise when it comes to their measurements and capacities as they are used to measure drugs administered to people. Insert molding is one of the few processes that ensure these instruments are made as accurately as possible.
- Electronic Devices: Electronic devices that range from wiring equipment and other plastic-based coverings are made through the insert molding process. Owing to how long cables may be, for instance, the fastest way to have them layered with insulation is through a quick process like insert molding that can handle batch processing.
- Plumbing Material: Plumbing is an essential part of construction, and plastic threaded inserts are used because they last longer and are easy to make. Through insert molding, the products can be scaled up and down at any time, making the process a versatile and reliable method to go with.
- Home Appliances: There’s no other palace where plastic products are used in huge numbers other than homes. From the kitchen to the kitchen, the living room to the bathroom, there’s always a plastic-based appliance used for convenience. Insert molding is one of the few processes that can be used to produce these high-demand home appliances in large numbers that can match the demand.
- Automotive Industry: Cars make use of plastic parts all the time as they are durable, lightweight, and easily replaceable. Through insert molding, these parts are designed with high precision to ensure they fit well with other car parts to assure safety once the vehicle rolls out of production.