Mold Design Service
At LXL Molding, we understand that superior mold design is the foundation of successful manufacturing. Our team of experienced designers and engineers is dedicated to creating high-precision molds that meet your exact specifications, ensuring the efficiency and quality of your production process.
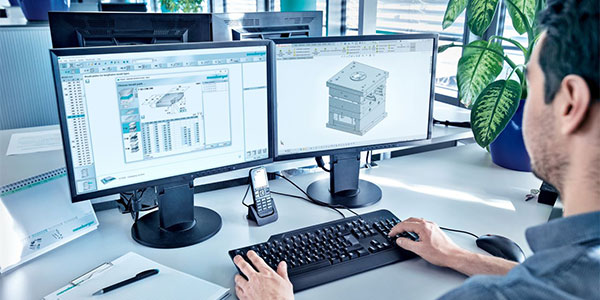
Our Mold Design Capabilities
The company specializes in the design and manufacturing of plastic molds, cold stamping molds, hot stamping molds, die-casting molds, smelting molds, and automated stamping molds. Additionally, there are experts in designing and manufacturing standard mold assemblies and detailed standard components, serving the mold-making industry with products such as standard mold bases, mold seats, block molds, and more.
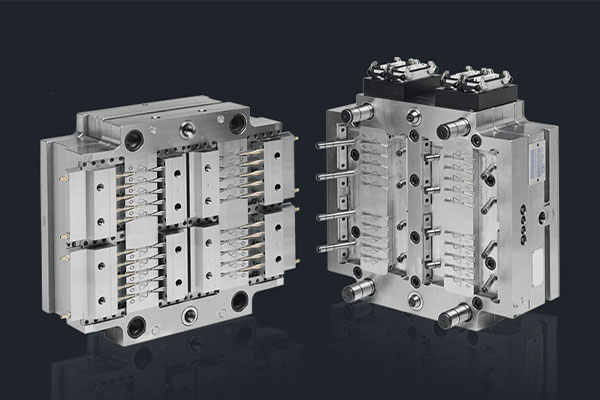
Precision Mold Manufacturing
Utilizing high-precision CNC machines and EDM (Electrical Discharge Machining) equipment, we ensure the accuracy and detail of our molds.
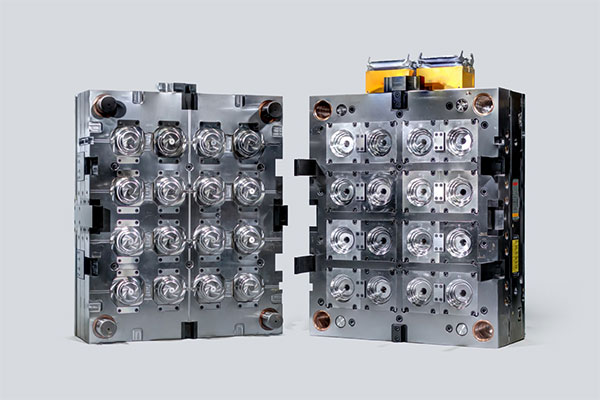
Multi-Cavity Mold Design
Optimizing production efficiency, we offer high-efficiency multi-cavity mold designs for mass production.
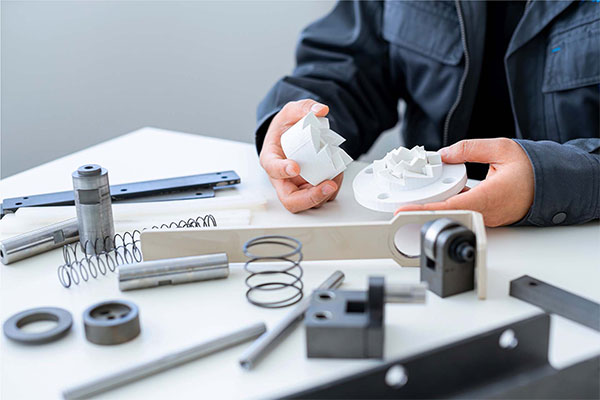
Rapid Prototyping
Through 3D printing and rapid prototyping tools, we shorten the time from concept to production.
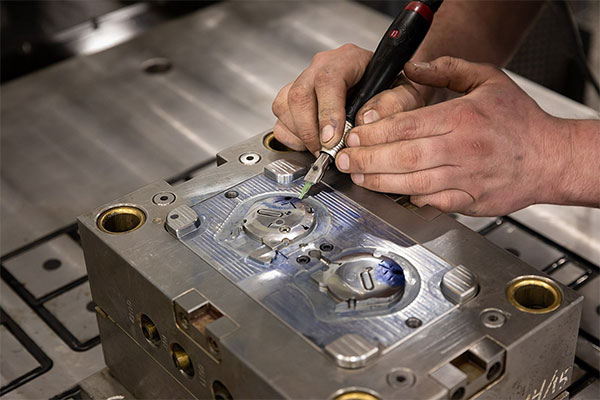
Mold Maintenance and Repair
We provide comprehensive mold maintenance and repair services to ensure long-term performance and durability of the molds.
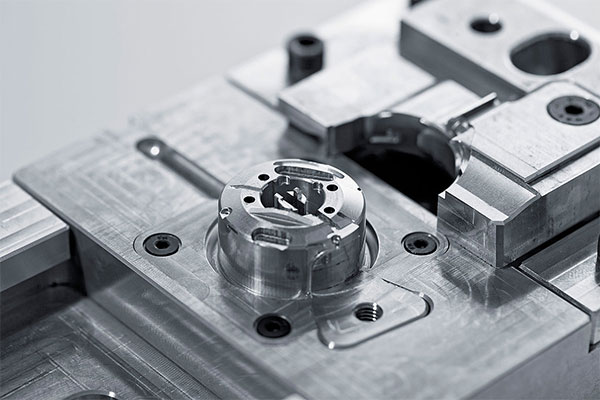
Customized Mold Solutions
Every project is unique, and so are our mold designs. We collaborate closely with you to understand your specific requirements, from part geometry and material selection to production volume and cycle time. Our custom mold solutions are tailored to optimize the manufacturing process, ensuring cost-effectiveness and consistency.
Advanced Design Software and Technology
We utilize the latest CAD/CAM software and 3D modeling techniques to create detailed, accurate mold designs. Our advanced technology allows us to simulate and analyze various factors, such as material flow, cooling, and potential stress points, to eliminate design flaws before the mold is produced.
Precision Engineering for Complex Designs
Our team specializes in designing molds for complex parts with intricate geometries and tight tolerances. We understand the challenges of high-precision molding and have the expertise to deliver designs that ensure the highest level of accuracy in the final product.
Design for Manufacturability (DFM) Analysis
Our Design for Manufacturability (DFM) analysis is a key part of our mold design process. We assess every aspect of the design to ensure it is optimized for efficient production. This includes evaluating material selection, mold structure, and potential production challenges to reduce costs and minimize waste.
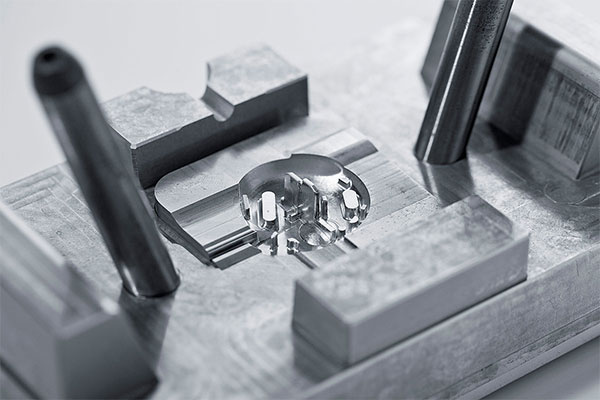
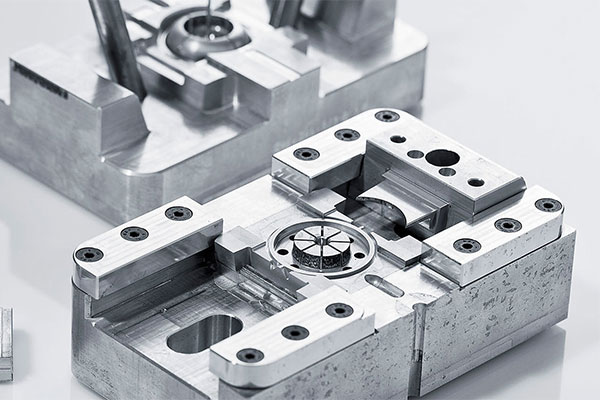
Multi-Cavity and Family Mold Design
For high-volume production, we offer multi-cavity and family mold designs that increase efficiency and reduce per-unit costs. Whether you need to produce identical parts or different components simultaneously, our mold designs are engineered to maximize productivity.
Rapid Prototyping and Testing
Before finalizing the mold design, we offer rapid prototyping services to create a physical model of the part. This allows us to conduct thorough testing and make any necessary adjustments to the design, ensuring that the final mold will perform flawlessly in production.
Our Mold Design Equipments
Medium-Speed Wire Cutting (5 Sets)
CNC (10 Sets)
Medium-Speed Wire Cutting (5 Sets)
EDM (8 Sets)
Precision Mirror-Finish EDM (2 Sets)
Grinding Machine (10 Sets)
Milling Machine (3 Sets)
Drilling Machine (1 Set)
Lathe Machine (1 Set)
Laser Printer (1 Set)
Laser Welding Machine (1 Set)
Why Choose LXL Molding for Mold Design?
- Experienced Design Team: Our team of seasoned designers and engineers brings years of industry experience to every project, ensuring top-quality mold designs.
- Cutting-Edge Technology: We leverage the latest design software and tools to create precise, efficient mold designs.
- Collaborative Approach: We work closely with our clients, valuing their input and ensuring that our designs meet their specific needs.
- Commitment to Quality: Quality is at the heart of everything we do, from initial design concepts to final mold production.